Table of Contents
ToggleSurface mount pick and place machines have become vital in the electronics manufacturing industry, known for their precision and speed in assembling electronic components onto printed circuit boards (PCBs). However, achieving the best results with these machines requires creating an ideal working environment. In this article, we’ll cover the essential conditions and standards that can enhance the performance and lifespan of surface mount pick and place machines.
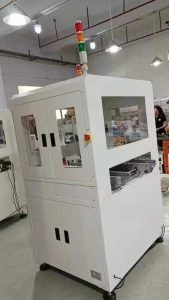
1. Temperature Control of Surface Mount Pick and Place Machines for Optimal Machine Performance
Maintaining a stable temperature is crucial for a surface mount pick and place machine as these machines operate best within a specific temperature range, usually between 22°C to 26°C (72°F to 79°F). Consistent temperature control (like our Cooling Conveyor for PCB) helps ensure that electronic components are placed accurately without the risk of damage from overheating or cold temperatures. Any fluctuations in temperature can cause mechanical issues and reduce placement accuracy, so utilizing an HVAC system that provides steady cooling and heating is essential for operational stability.
2. Humidity Levels: Avoiding Static and Corrosion
Humidity plays a significant role as high humidity can lead to corrosion, while low humidity increases the risk of static electricity, which can damage sensitive electronic components. Ideally, humidity levels should remain between 40% and 60%. Installing a humidity control system can help maintain the recommended levels, preventing electrical discharge and preserving component quality during the placement process.
3. Air Quality Control to Minimize Contamination
Dust and other airborne particles can seriously impact the performance of pick-and-place machines. When dust particles settle on components or circuit boards, they interfere with the machine’s vision systems, causing placement errors. Keeping the room air clean reduces the likelihood of contamination, so consider using HEPA filters and maintaining positive air pressure to keep particles out. This setup ensures that the machine operates smoothly and increases assembly precision.
4. Consistent and Reliable Power Supply
A stable and uninterrupted power source is crucial for the operation of a surface mount pick and place machine. Power surges or drops can disrupt machine function, causing delays or inaccuracies in component placement. A reliable uninterruptible power supply (UPS) system can protect the machine from power fluctuations, providing a consistent voltage level that ensures smooth and uninterrupted operations.
5. Flooring Requirements for Vibration Reduction
Vibrations from surrounding machinery or even building structures can disrupt the sensitive operations of pick and place machines. Installing anti-vibration flooring or isolation platforms under the machine is an effective way to minimize the impact of vibrations. These measures help maintain placement accuracy, reduce mechanical stress on the equipment, and extend the machine’s life.
6. Controlled Lighting to Enhance Machine Vision
The machine vision system in surface mount pick and place machines relies on precise lighting to accurately detect components and PCB markings. Excessive or insufficient lighting can disrupt the system’s performance, leading to alignment errors. Use LED lights or other stable lighting sources with adjustable brightness to maintain consistent light levels, ensuring the machine vision system works optimally without interference from external lighting variations.
7. Proper Ventilation for Heat Management
The heat generated by the machine and surrounding equipment can accumulate in the room, leading to increased temperatures and reducing the machine’s efficiency. Proper ventilation, either through an exhaust fan system or an air exchange system, will help dissipate excess heat. This setup not only prevents overheating but also reduces energy costs by lowering the demand for HVAC systems.
Conclusion
A surface mount pick and place machine‘s performance depends on various environmental factors, including temperature, humidity, air quality, and ESD protection. By maintaining optimal conditions and conducting regular maintenance, manufacturers can maximize machine efficiency, reduce the risk of errors, and extend the lifespan of their equipment. Creating an ideal working environment for these machines not only enhances production quality but also contributes to operational cost savings in the long run.
For more information, visit our website by clicking here!